Los tubos soldados longitudinalmente están hechos de placas o tiras de acero que se doblan y luego se sueldan. Según la forma de soldadura, se divide en tubería soldada con costura recta y tubería soldada en espiral . Según el propósito, se divide en tubería soldada general, tubería soldada galvanizada, tubería soldada por soplado de oxígeno, revestimiento de alambre, tubería soldada métrica, tubería loca, tubería de bomba de pozo profundo, tubería de automóvil, tubería de transformador, tubería de pared delgada soldada eléctricamente, tubería de forma especial soldada eléctricamente y tubería soldada en espiral.
Ⅰ Descripción del principal proceso de producción de tubería soldada longitudinal de gran diámetro :
1. Inspección de la placa: después de que la placa de acero utilizada para fabricar tubos de acero de costura recta soldados por arco sumergido de gran diámetro ingresa a la línea de producción, toda la placa se inspecciona primero por ultrasonido;
2. Fresado de bordes: use la fresadora de bordes para realizar un fresado de doble cara en ambos bordes de la placa de acero para lograr el ancho de placa requerido, el paralelismo del borde de la placa y la forma de la ranura;
3. Predoblado: use una máquina predobladora para predoblar el borde de la placa de modo que el borde de la placa tenga una curvatura que cumpla con los requisitos;
4. Formación: en la máquina formadora JCO, la primera mitad de la placa de acero predoblada se estampa en forma de "J" mediante varios pasos, y luego la otra mitad de la placa de acero también se dobla en forma de "C". y finalmente se forma la abertura. "O"
5. Pre-soldadura: Haga la costura de tubería de acero soldada con costura recta formada y use soldadura con protección de gas (MAG) para soldadura continua;
6. Soldadura interna: use soldadura por arco sumergido de alambres múltiples en tándem (hasta cuatro alambres) para soldar en el interior de la tubería de acero con costura recta;
7. Soldadura externa: use soldadura por arco sumergido de alambres múltiples en tándem para soldar en el exterior de la tubería de acero soldada por arco sumergido con costura recta;
8. Inspección ultrasónica Ⅰ: inspección del 100% de las soldaduras internas y externas de la tubería de acero soldada con costura recta y el metal base en ambos lados de la soldadura;
9. Inspección de rayos X Ⅰ: 100% inspección de TV industrial de rayos X para soldaduras internas y externas, utilizando un sistema de procesamiento de imágenes para garantizar la sensibilidad de la detección de fallas;
10. Expansión del diámetro: expanda la longitud total de la tubería de acero con costura recta soldada por arco sumergido para mejorar la precisión dimensional de la tubería de acero y mejorar la distribución de la tensión interna de la tubería de acero;
11. Prueba hidrostática: en la máquina de prueba hidrostática, inspeccione las tuberías de acero expandido una por una para asegurarse de que las tuberías de acero cumplan con la presión de prueba requerida por la norma. La máquina tiene funciones automáticas de grabación y almacenamiento;
12. Biselado: procese el extremo del tubo de acero calificado para cumplir con el tamaño de bisel requerido del extremo del tubo;
13. Inspección ultrasónica Ⅱ: realice una inspección ultrasónica una por una nuevamente para verificar los posibles defectos de las tuberías de acero soldadas con costura recta después de la expansión del diámetro y la presión hidráulica;
14. X-ray inspection II: Carry out X-ray industrial TV inspection and filming of pipe end welds on steel pipes after diameter expansion and hydrostatic test;
15. Tube end magnetic particle inspection: This inspection is carried out to find tube end defects;
16. Anti-corrosion and coating: The qualified steel pipes are anti-corrosion and coating according to user requirements.
Ⅱ Analysis and description of dry welding technology for large-diameter thick-walled welded pipes:
U-shaped grooves or composite grooves are often used for automatic welding of large-diameter and thick-walled (greater than 21mm) pipelines. Due to the time-consuming and labor-intensive processing of U-shaped grooves and composite grooves, the welding efficiency of pipelines is restricted. V-groove processing is simple, time-saving and labor-saving, but when large-diameter and thick-walled pipeline V-groove automatic welding, if the welding process parameters are not selected properly, welding defects will occur.
The welding method adopts STT root welding + CRC-P260 automatic welding machine for heat welding, filling and covering. Welding equipment: Lincoln STT welding machine, Lincoln DC-400, CRC-P260 automatic welding machine. Shielding gas: STT root welding shielding gas 100% CO2, fully automatic welding shielding gas 80% Ar+20% CO2.
Composite groove or U-shaped groove is commonly used in automatic welding, and V-shaped groove can also be used in pipelines with small wall thickness. Their common feature is that the gap on the groove is small. The wall thickness of the second line of the West-East Gas Pipeline is 21.0mm, and the upper opening width of the V-shaped groove is about 22mm, which is close to the swing limit of the CRC-P260 welding torch. Such a groove pattern is a great challenge for automatic welding. The welding process parameters of the automatic welding test were determined according to past experience.
The automatic welding test was carried out with the above parameters. During the test welding, it was found that automatic welds were prone to defects, such as unfused interlayers, unfused side walls, dense pores, and excess height of the overhead welding position.
In order to ensure a good cover forming effect, the cover welding should be done with a smaller
At the same time of welding speed, reduce the swing frequency of the welding torch as much as possible, so that the welding seam on the cover surface is thin and wide, thereby reducing the existence time of the molten pool and achieving the purpose of reducing the residual height of the overhead welding position. According to the test welding results and analysis, the process parameters of STT root welding + CRC automatic welding filling and covering of the connecting line of the second West-East Gas Pipeline were finally determined. Welded according to the welding parameters in Table 3, the weld seam has no defects such as pores, cracks, and lack of fusion after inspection, and the surface shape of the weld seam is good.
The mechanical properties of the welds have been tested by the Welding Technology Center of the China Petroleum and Natural Gas Pipeline Science Research Institute, and all indicators meet the construction requirements of the second line of the West-East Gas Pipeline. The successful application of STT root welding + CRC-P260 automatic welding on large-diameter, thick-walled (V-shaped groove) pipelines fully reflects the characteristics of high-quality, high-efficiency, and low-labor intensity of automatic welding technology.
Ⅲ、Technical requirements and quality inspection of straight seam welded pipes:
According to GB3092 "Welded Steel Pipes for Low-Pressure Fluid Transmission", the nominal diameter of the welded pipe is 6~150mm, the nominal wall thickness is 2.0~6.0mm, and the length of the welded pipe is usually 4~10 meters. factory. The surface quality of the steel pipe should be smooth, and defects such as folding, cracks, delamination, and lap welding are not allowed. The surface of the steel pipe is allowed to have minor defects such as scratches, scratches, weld misalignment, burns and scars that do not exceed the negative deviation of the wall thickness. The thickening of the wall thickness at the weld and the existence of inner seam welding reinforcement are allowed. Welded steel pipes should be subjected to mechanical performance test, flattening test and flaring test, and must meet the requirements of the standard.
The steel pipe should be able to withstand a certain internal pressure, and if necessary, carry out a 2.5Mpa pressure test to keep it leak-free for one minute. The method of eddy current flaw detection is allowed to replace the hydrostatic test. The eddy current flaw detection is carried out according to the standard of GB7735 "Steel tube eddy current flaw detection inspection method". The eddy current flaw detection method is to fix the probe on the frame, keep a distance of 3~5mm between the flaw detection and the weld seam, and conduct a comprehensive scan of the weld seam by the rapid movement of the steel pipe. The flaw detection signal is automatically processed and sorted by the eddy current flaw detector. To achieve the purpose of flaw detection. The welded pipe after the flaw detection is cut off according to the specified length with a flying saw, and it is rolled off the assembly line through the turning frame. Both ends of the steel pipe should be chamfered with flat ends, printed with marks, and the finished pipes are packed in hexagonal bundles before leaving the factory.
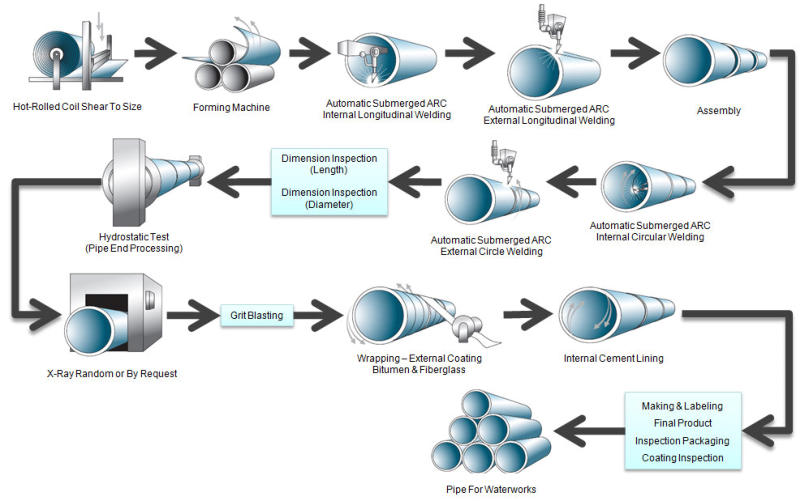