42CrMo steel is an ultra-high-strength steel with high strength and toughness, good hardenability, no obvious temper brittleness, high fatigue limit and multiple impact resistance after quenching and tempering, and good low-temperature impact toughness. This steel is suitable for manufacturing large and medium-sized plastic molds that require certain strength and toughness.
42CrMo alloy tube
Its corresponding international standard organization grade: 42CrMo4; corresponding Japanese grade: SCM440;
Corresponding German grade: 42CrMo4; Approximate corresponding American grade: 4140
●Characteristics and scope of application:
High strength and hardenability, good toughness, small deformation during quenching, high creep strength and durable strength at high temperature. It is used to manufacture forgings that require higher strength and larger quenched and tempered sections than 35CrMo steel, such as large gears for locomotive traction, supercharger transmission gears, rear axles, highly loaded connecting rods and spring clips, and can also be used for Oil deep well drill pipe joints and fishing tools below 2000m, and can be used for bending machine molds, etc.
●Chemical composition:
Carbon C: 0.38~0.45
Silicon Si: 0.17~0.37
Manganese Mn: 0.50~0.80
Sulfur S: Allowable residual content ≤ 0.035
Phosphorus P: allowable residual content ≤ 0.035
Chromium Cr: 0.90~1.20
Nickel Ni: Allowable residual content ≤ 0.030
Copper Cu: Allowable residual content ≤ 0.030
Molybdenum Mo: 0.15~0.25
●Mechanical properties:
Tensile strength σb (MPa): ≥1080(110)
Yield strength σs (MPa): ≥930(95)
Elongation δ5 (%): ≥12
Reduction of area ψ (%): ≥45
Impact energy Akv (J): ≥63
Impact toughness value αkv (J/cm2): ≥78(8)
Hardness: ≤217HB
Sample size: sample blank size is 25mm
42CrMo heat treatment:
Annealing annealing No.1 "Annealing at 760±10℃, furnace cooling to 400℃ and air cooling.
HB220-230
Normalize No.4 Normalize at 860±10°C, and air cool after taking out the furnace.
Quenching+tempering No.5 Quenching with water or oil at 840±10°C (depending on the complexity of the product shape), tempering at 680-700°C. HB<217
Quenching+tempering No.6 Quenching oil at 840±10°C, then tempering at 470°C. HRC41-45
Quenching+tempering No.7 Quenching oil at 840±10°C, then tempering at 480°C. HRC35-45
Quenching+tempering No.8 Quenching oil at 850°C, then tempering at 510°C. HRC38-42
Quenching+tempering No.9 Quenching oil at 850°C, then tempering at 500°C. HRC40-43
Quenching+tempering No.10 Quenching oil at 850°C, then tempering at 510°C. HRC36-42
Quenching+tempering No.11 Quenching oil at 850°C, then tempering at 560°C. HRC32-36
Quenching+tempering No.12 Quenching oil at 860°C, then tempering at 390°C. HRC48-52
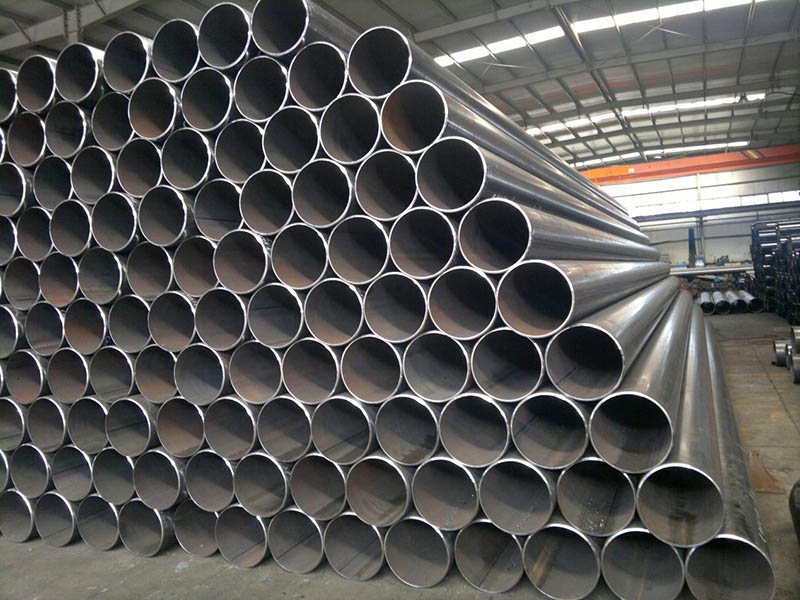